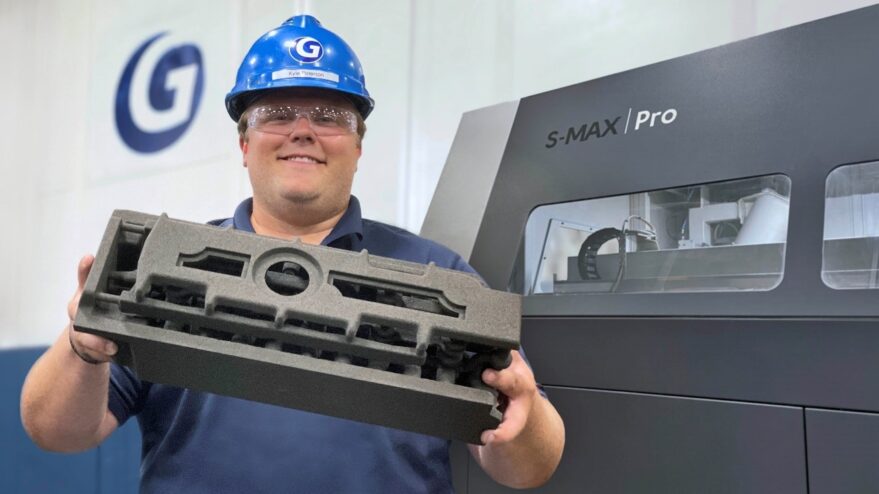
Iron Ingenuity Applied: 3D Sand Printing at Grede
October 23, 2024
We’re pleased to share that our foundry in Biscoe, North Carolina recently added its first 3D sand printer to print complex sand cores for our castings. Our foundry in Iron Mountain, Michigan also has three 3D sand printers.
It’s exciting to see us expand this technology to more plants in our network. Because of this, below is an article all about what 3D printers are, how they work, and why we use them in our foundries.
What are 3D Sand Printers?
3D sand printers harness the power of additive manufacturing—the process of creating an object by building it one layer at a time— to craft intricate sand cores for metalcasting. Using digital designs as blueprints, these printers meticulously build up layers of sand, creating cores with unparalleled precision and complexity.
A foundry sand core is a sand-based structure used in metalcasting to form internal cavities, hollow sections, or intricate shapes as the base for the casting. Placed in the mold before pouring molten metal, the sand core is removed after the metal solidifies, leaving the desired shape.
Sand cores traditionally rely on tooling to create the core through manual processes, which can be time-consuming, less precise, and wasteful, while 3D-printed cores offer faster production, greater design flexibility, higher precision, and reduced material waste, making them more efficient and environmentally friendly.
Grede Iron Mountain in Michigan remains ahead of the competition as one of the first foundries to incorporate 3D printing as a production option.
Grede’s 3D Sand Printing Journey
Grede started using a 3D sand printer, the ExOne S-Max, in January 2018 and now operates three 3D sand printers full-time every day at our foundry in Iron Mountain, Michigan. In August 2024, we installed our fourth 3D sand printer at Grede, which is our first 3D printer at Grede Biscoe in North Carolina.
These machines have fundamentally changed how we produce cores, enabling us to shorten lead times and improve production flexibility. Today, 40% of Iron Mountain’s casting tonnage is produced by our 3D printing machines, solidifying our position as a leader in the foundry industry.
Timeline
- 2004-2016: Grede reviews 3D sand capabilities and works through feasibility studies
- 2018: 3D Printer #1 installed – First full production at Iron Mountain foundry in Michigan
- 2021: 3D Printer #2 installed – Capacity full in first three months in Iron Mountain
- 2023: 3D Printer #3 installed – Capacity full day one in Iron Mountain
- 2024: 3D Printer #4 installed – First 3D printer at our Biscoe facility in North Carolina
Traditional Tooling vs. 3D Printing
By eliminating traditional tooling, we can offer faster, cleaner, and more cost-effective solutions.
The turnaround time on first article castings has dramatically shortened with 3D printed options. 3D printers are clean, quiet, temperature controlled, and are in a lab-style environment, as opposed to the traditional tooling option.
Traditional Tooling Environment:
Before 3D printers, we used shellcore machines in an environment that is hot, dirty, loud, repetitive, physically demanding, and difficult to change the tooling.
3D Print Environment:
Iron Mountain’s 3D Printing Room:
Biscoe’s 3D Printing Room:
Why 3D Sand Printing Technology?
There are several benefits to 3D printing technology, including:
- Complex Geometries: Allows for highly intricate and complex core shapes otherwise difficult or impossible to achieve using traditional methods.
- Cost Efficiency: Reduces the need for expensive tooling and molds, leading to lower upfront costs, especially for low-volume or custom parts.
- Material Savings: The process is additive, meaning the material is only used where needed, minimizing waste and making it more resource-efficient.
- Faster Prototyping and Production: Accelerates the design-to-production timeline, allowing for faster iterations, prototyping, and production runs.
- Design Flexibility: Engineers have greater flexibility in their designs, as 3D printing can produce internal cavities, undercuts, and hollow sections without the constraints of traditional manufacturing.
- Improved Casting Quality: Precision of 3D printed cores leads to higher accuracy in the final cast products, improving quality and reducing the need for post-processing.
- Sustainability: Sustainable processes by reducing waste, energy consumption, and material use, contributing to a lower carbon footprint.
3D Printing Saves Energy
Our 3D printers reduce material waste, minimize energy consumption, and lower emissions. In fact, our 3D sand printing has saved enough energy to power the entire city of Iron Mountain, Michigan! It saves 5.6 million gallons of water annually, reduces electricity consumption by 235,880 kWh, and lowers natural gas usage by 192,000 Mcf.
3D printing materials are recyclable, and the rapid prototyping capabilities of 3D printing enable foundries to test and refine core designs more quickly.
As a result, 3D sand printing contributes to a more environmentally friendly and economically efficient operation.
Case Study: 3D Printing Success with Hydraulic Pumps
In the past, hydraulic pump cores required multiple assembly steps, leading to high scrap rates and production inefficiencies. With 3D printing, we scanned existing cores and assembled them digitally, resulting in a 300-piece casting run with only 12% scrap—free from core-related defects.
Meet the Foundry of the Future: Grede’s Vision for 3D Printing
Grede is leading the charge in transforming the foundry industry. Our investment in 3D printing isn’t just about staying competitive—it’s about redefining the possibilities of metalcasting. From automotive to heavy truck and industrial applications, we help our customers get to market faster with better products.
Our Promise: Iron Ingenuity
At Grede, we combine iron casting expertise with cutting-edge technology to deliver dependable solutions for an evolving world. By embracing additive manufacturing, we create new opportunities for our customers, drive sustainability, and redefine what’s possible in metalcasting.