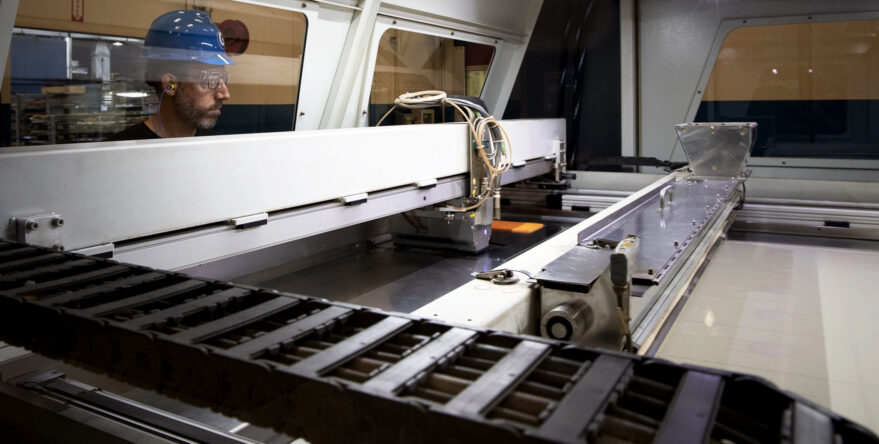
Innovation Applied: 3D Printing Bearing Housings & Cored Products at Grede
April 7, 2022
The process of manufacturing bearing housings, valve bodies and other complex cored products has traditionally required the assembly of multiple cores.
Today, advances in 3D printing technology are enabling foundries like Grede to make complex sand cores in a more efficient manner.
What was once a lengthy process requiring multiple steps and manual labor can now be significantly shortened.
What are bearing housings and how do they work?
Before examining how the process of making bearing housings and other cored products has changed, and describing the benefits of 3D printing bearing housings, it’s helpful to define what they’re used for.
“A bearing housing is one of three major sections of a turbocharger, which is typically used to increase horsepower,” says Steve Sechrist, vice president of sales for Grede.
“The function of a turbocharger is to take the waste exhaust gas and use it to generate more energy. The bearing housing is the middle section that contains a shaft with a turbine wheel on one end and an impeller wheel on the other. The hot gas turns the turbine wheel, which in turn drives the impeller, pulling forced outside air into the engine.”
Because they are not dealing with the highest temperature exhaust gasses that turbine housings would handle, bearing housings are typically manufactured from grey iron. One of the common applications for bearing housings are commercial vehicle engines.
“Grede is the largest producer of commercial vehicle bearing housings with variable geometry in the United States, and potentially in all of North America,” says Jerry Smith, senior accounts manager for Grede. “Our investment in 3D printing machines to produce these housings, as well as valve bodies and other highly complex cored products, provides flexibility and positions Grede well in the market.”
Where other foundries have typically outsourced 3D core printing to third parties, Grede has been on the leading edge of bringing additive manufacturing in house.
This 3D printed valve body core replaces three individual cores that would have been glued together in a traditional core making process.
“Bringing 3D printing into our internal operations has revitalized our position in the industrial market space,” says Sechrist. “This is especially true when it comes to products like valve bodies with complicated internal passageways that involve assembling four, five, six or even 10 cores together. Being able to shorten our casting process through additive manufacturing has put Grede a few years ahead of the curve. Where other foundries are just now investing in 3D printing technology, we’ve already been there for several years.”
How were bearing housings and other products with core assemblies traditionally made?
Before additive manufacturing, making bearing housings, valve bodies and other cored products with complex geometry was a manual process.
Multiple cores were produced and assembled by hand for these complex geometries. The process required time for gluing and assembly.
“The conventional process for core making with complex geometry required multiple core machines and assembly of the various cores to make the required core assembly for the molding process,” says Smith. “It’s a tried-and-true approach that works but is labor intensive.”
How are bearing housings and other cored products with complex geometries made at Grede now?
Today, one of the innovative uses of 3D printing at Grede is letting a machine do all that intricate work.
“Advancements in 3D printing allow us to create intricate cores in one process and with an incredibly high degree of precision and accuracy,” says Smith. “With additive manufacturing, manual gluing and assembly is removed.”
The result? Efficiencies and cost savings that can be passed on to customers.
What are the benefits of 3D printing?
The benefits of using 3D printing to create bearing housings, as well as a wide variety of products requiring complex cores, are fairly straightforward.
“Whereas people need to stop, a 3D printer designed for this kind of work, like the ExOne binder jetting machines Grede uses, can run 24/7,” says Kyle Peterson, Iron Mountain foundry engineering manager for Grede. “It’s economical, efficient and accurate.”
Additional benefits include:
- Highly cored, intricate castings, including hydraulic valves and transmission components can be printed from CAD models without tooling.
- High volumes of complex cores and assemblies can be produced quickly and accurately.
- More flexible designs can be accommodated.
- Immediate design changes can be implemented.
- Scrap waste is reduced.
- Fewer materials are used.
- Less labor is required.
The process works as resin micro-droplets are deposited by the machine onto thin layers of sand. Therefore, assembly operations are eliminated entirely.
“Another benefit we’re seeing is that prototypes can be created quite quickly, reducing overall time to market for our customers,” says Sechrist. “By decreasing the time required to build prototypes, customers can evaluate new products and design changes sooner.”
How does 3D printing support sustainability?
In some ways, Grede is in the recycling business. Not only does some of the iron Grede uses come from scrap metal, but the use of 3D also printing itself creates less scrap. Additionally, sand used in the core-making process can be recycled and used again on additional molds.
“Our goal is to reclaim 100 percent of the sand we use. We’re well on our way to achieving that goal by recycling our printed cores that break down during the casting process and reusing the resultant material as mold sand,” says Smith. “It goes through a conveyor, gets reconstituted and treated again and then becomes part of the sand used for future molds.”
An additional environmental benefit is that less energy is used with 3D printing than traditional bearing housing mold production.
Finally, because the 3D-printing process does not use heat to create a core, chemical burn-off that occurs with other core-making processes requiring intense heat is eliminated.
Without intense heat, as in some other core making processes, the burn-off from those chemicals is eliminated.
Future innovations at Grede
Beyond more efficient core-mold manufacturing, 3D printing is advancing other processes at Grede.
“Grede is a player in a number of markets from automotive to heavy truck and industrial in ways that we weren’t before,” says Sechrist. “We’re helping our customers get to market faster, with innovative designs, which is exciting.”